Description/ Model | Speed | Technical | Format Range | Applications | Benefits |
---|
Vario GO558 S
Vario GO558 L
Vario GO558 1
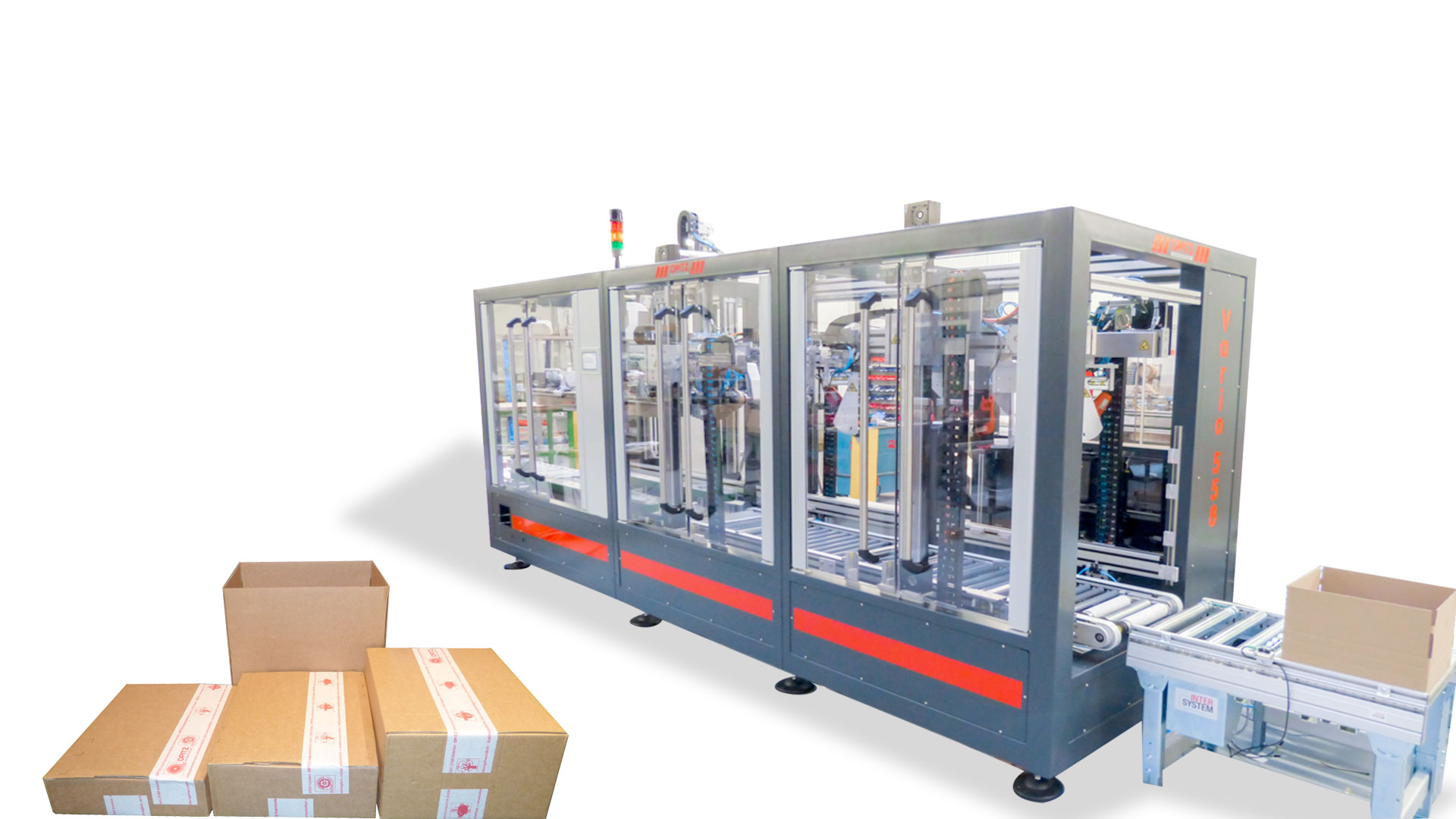 Volume Reducing case taping machine | 10 cartons/minute
6-8 cartons/minute
6 | Sensors detect incoming case footprint, height and content height
Knives slit creases to reduce height
Gummed tape dispenser seals folded flaps
Automatic volume reduction | Length 200 - 600 mm , Width 200 - 400 mm , Height 60 - 500 mm
Length 200 - 800 mm , Width 20 | - Logistics and Dispatch
- Warehouse goods out
- Consumer goods
- Internet order fulfilment
| - Reduced fill good costs
- Reduced transport costs
- Recyclable paper tape application possible
- Tamper evident gummed taped possible
- Knife free box opening with tear strip
- Additional taping positions optional
|
GO 795 Single
GO 795 Twin
GO 795 Triple
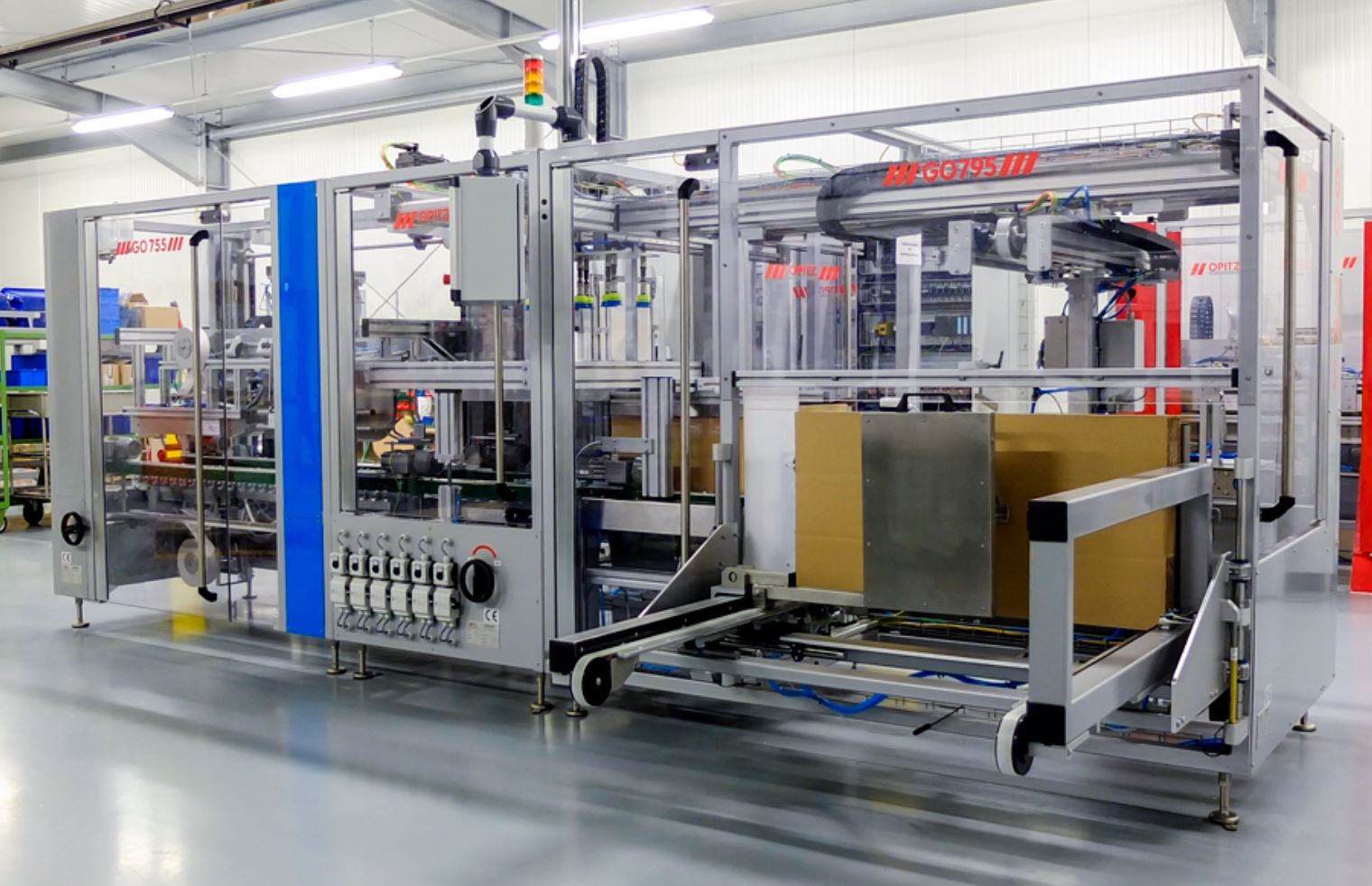 Flexible Case Erectors | 12
10
8
| Roller Doors to allow maintenance whilst running
Macralon Guards
Stainless Steel design upon request | | - Disptach
- Warehouse
- Low output per line multi-line applications
- Hand Loading
| - less than 5 minute changeover
- Up to 3 different case sizes simultaneously
- Changeover one case while others still running
|
GO750
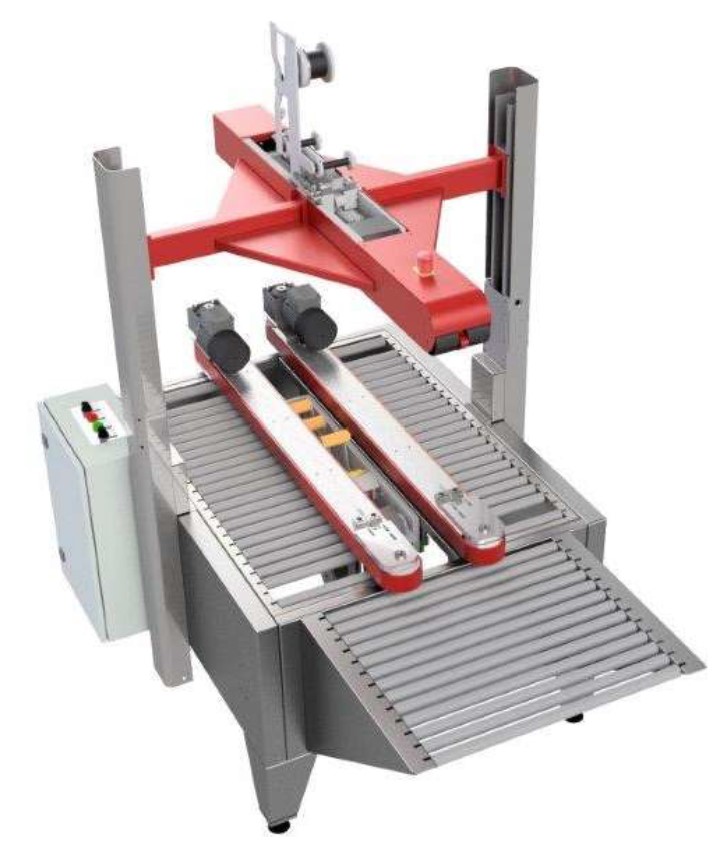 Entry Level Case Taper for Gummed Tape | Up to 10 cases per minute | Automatically Adjusts to Case Dimensions
Top and Bottom Flap Closure
Pneumatically controlled tape dispensers
Simple PLC to recognise input | min 250 x 150 x 180 mm
max 800 x 600 x 650 mm | - Warehouse Dispatch Operations
- Manufacturing environments
- Entry Level
| - No format changeover needed
- Environmentally friendly Water Activated Gummed Tape
- Compact footprint
- Easy Reel Change
- Operator feeding
|
GO 890
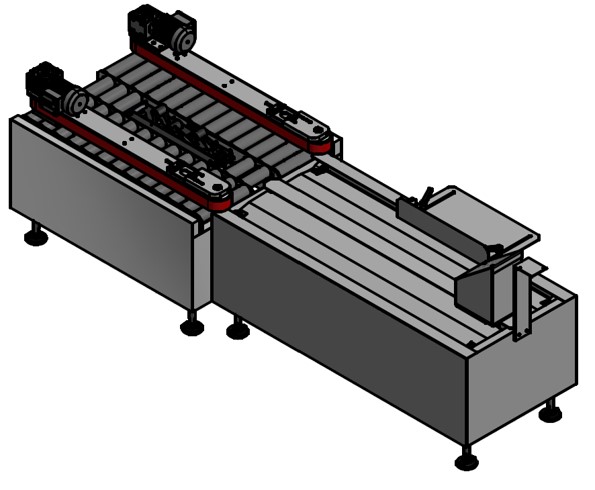 Semi Automatic Case Erector | Determined by Operator | | Length: 200 - 700 mm
Width: 150 - 500 mm
Height: As required | - Dispatch operations
- Manual packing operations
| - Fast changeover
- Flexible size range
|
Genix-XP
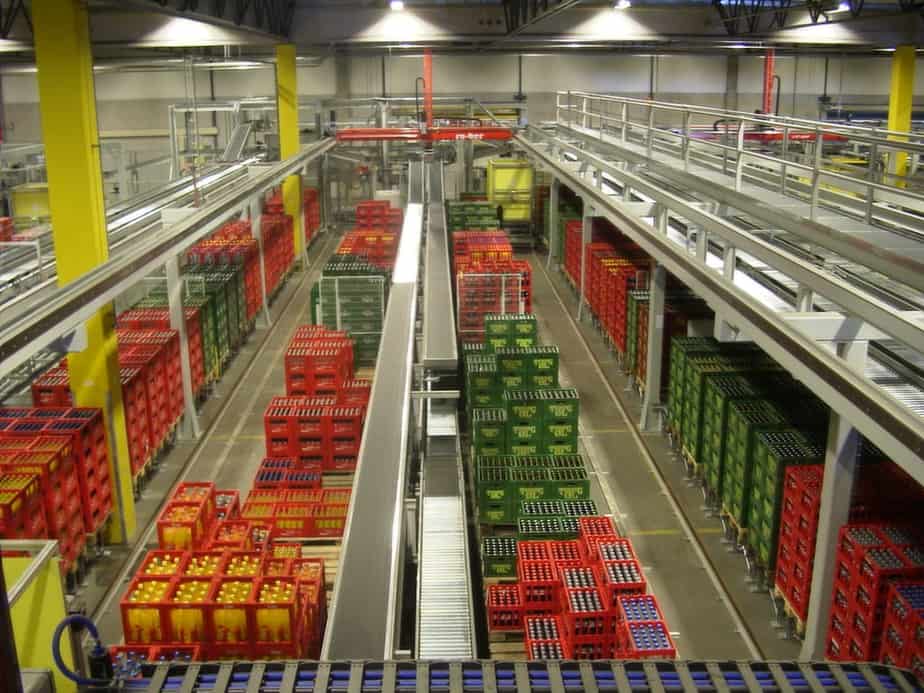 Warehouse Material Handling and Buffer Systems | 2m/s subject to payload | Extra Wide - up to 20 m x 40 m
Payloads up to 1000 Kg
Point to point motion | | - Crate Storage
- Tray Storage
- Empty Crate Buffers
- Tray washer buffers
- Cold Stores management
| - Fast throughput
- Not restricted to area
- Easily expandable
|
FP 150, LP150, FP 300, LP 300
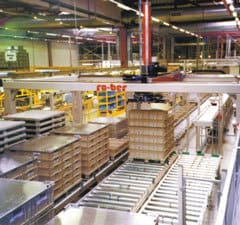 Palletisers and De Palletisers | | | Up to 10 x 40 m Working Area | - Order picking
- Tote, case, can or bottle handling
- Multiple line palletisation
| - Direct point to point movement
- Expandable system
|
FP300, FP150
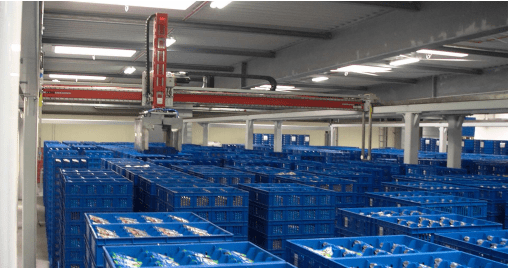 Automated Warehouse using Gantry Robots | Up to 250 picks/hr | | Wide Areas, Up to 12 x 40 m | - Warehouse
- Bakery
- Cold Store
| - Up to 4 Robots sharing the working Area
- High storage density.
- Comparatively low maintenance when compared to mini load systems.
|
FP150, FP300
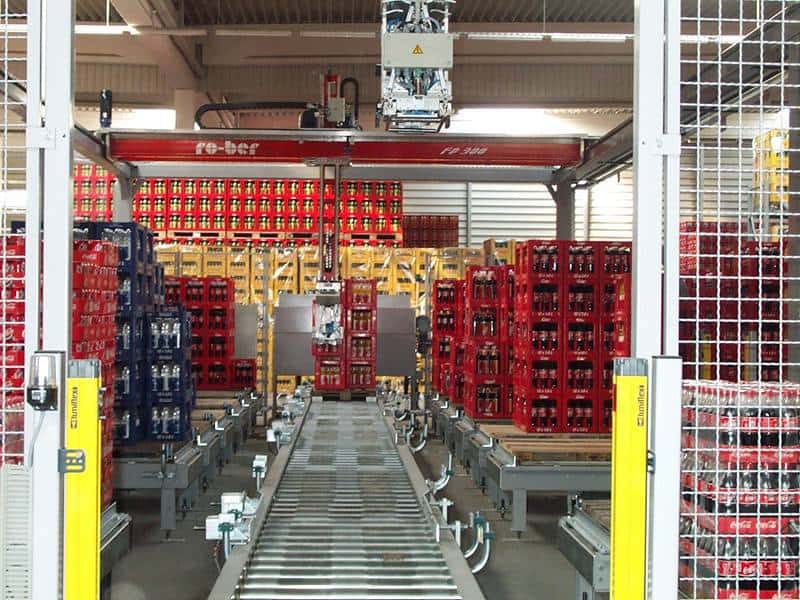 Order Picking Robots | Subject to Configuration | | Areas up to 10 x 40 metres | | - Multi-product gripper
- Modular System
- Automatic layer scheme generation using Ro-Mix software
- High through puts (200 pallets per hour)
- Different pallet sizes
- Integrated wrapping possible
|
LP150
LP300
FP150
FP300
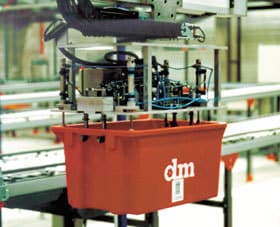 Gantry Robots | Up to 2 m/sec | All XYZ movements of the Gantry Robot are controlled by servo drives. Therefore our Gantry system is accurate to a couple of millimetres
Steel reinforced toothed belts drive the axes. These are precise, quiet in operation, long lasting and easy to maintain.
Up to 4 Gantry Robots can share the same working area. This makes our Gantry system ideal for applications such as palletising and order picking as multiple robots have Different solutions available to minimise the head height required by the Gantry system. The standard Gantry Robot has a fixed axis that is at least as long as the height of the pallet. An optional telescopic axis can half the Z axis and the Z-NIX axis can reduce the height above the pallet to little more than that required by the Gripper.
Our software is open source, -no black box- based on Beckhoff Soft PLC and programmed in Codesys.
Gripping can be by Vacuum, Magnet or Mechanical Clamping in rows, stacks or as individual packs. | | - Palletising across Multiple Lines
- De-Palletising
- Storing totes
- Buffering Cases or Totes
- Central palletisers
| - Compact layout
- Size and throughput expandable in the future
- Direct fast, point to point movements
- Evenly distributed floor loading
- Single gantry robot can handle multiple lines to palletise move or store
|
Stacker
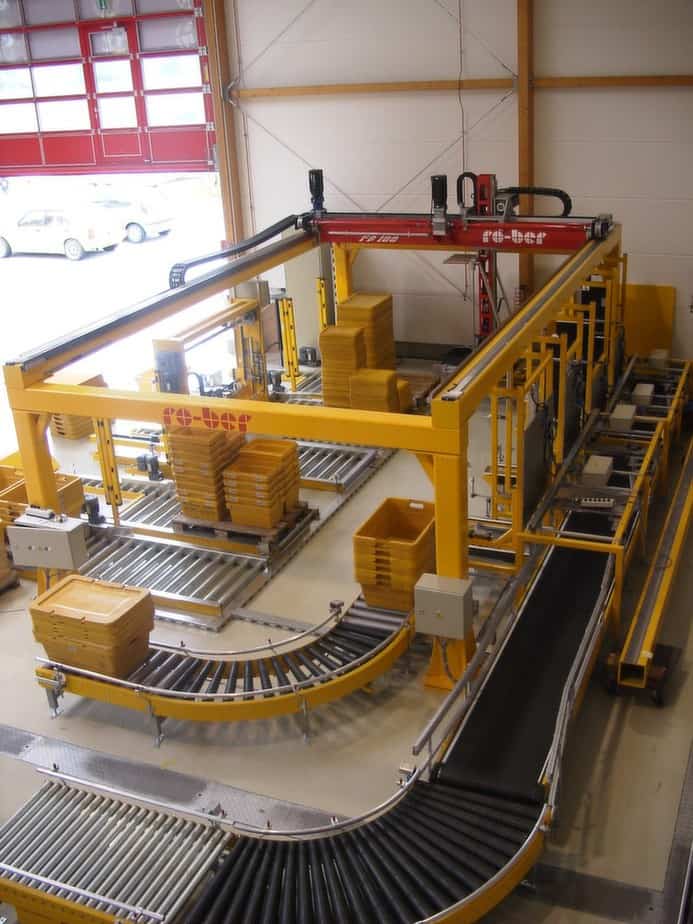 Tote Stacking, De stacking and Palletising | Up to 1800 Crates per hour
| | 300 x 200 x 100mm to 800 x 600 x 400mm | - Totes
- Crates
- Bananna Boxes
| - Optional Automatic Format Changeover
- Intergrated Conveyors
- Stacking or De-Stacking
|